Ron Earp
Administrator
When I was over at WallyWorld on Friday I picked up pieces for another driver cooling system. We have DR COOL but we'll need another one for Jeff G's car or for mine if the weight of DR COOL is too much for the build.
$8 cooler with screw lid, $19 live well pump, and $20 of dry break connectors. I whipped part of the system up.
$8 cooler with screw lid, $19 live well pump, and $20 of dry break connectors. I whipped part of the system up.
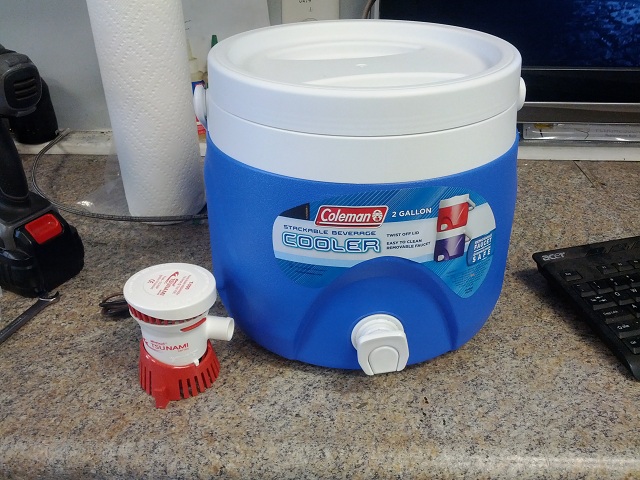
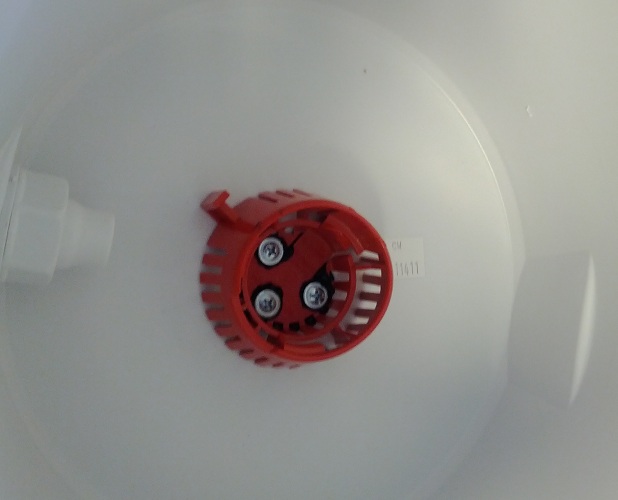
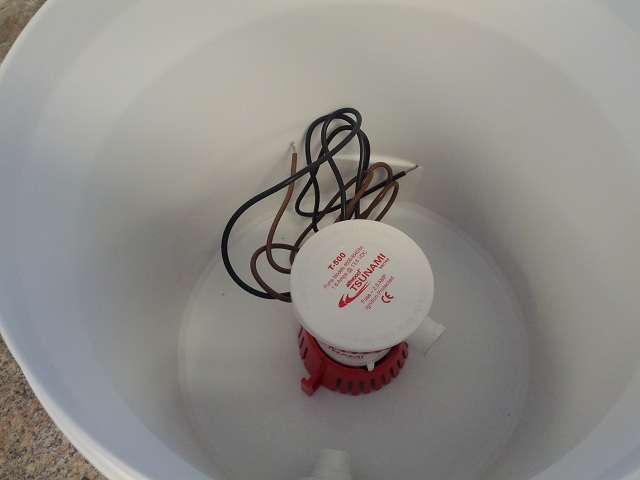
Last edited: